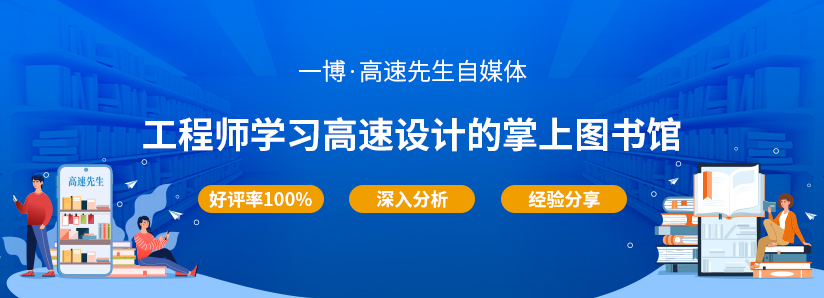
PCB厚铜板的设计,这一点一定要注意
发布时间:2022-08-15 09:25
作者:37000Cm威尼斯高速先生成员 王辉东
林如烟总是说:“线路板上的成品铜厚越厚,线宽线距要足够。”
她的好友佳妮说:“必须必须。”
暗恋佳妮的小齐也总是笑嘻嘻的附和道:“美女说的都是对的。”
至于原因是什么,他只知道个大概,但是他也讲不出个具体一二三。
然而现实中有些事情总是令人猝不及防。
小齐在做市场。
客户说我有一个14层板,天天熬夜加班设计了两个月,交期很急,帮忙赶一下。
小齐说可以。

光看客户的局部图纸就知道PCB很密,设计确实不易,更是考验工厂的加工能力。
但是接到板子后,工程师一评估,问题就来了。
PCB内层有2OZ铜厚的要求,内层设计有3.5/3.5mil的线宽线距,超出工艺加工能力。
建议客户把内层铜厚修改成1OZ,客户说仿真做过了不能修改,要满足载流能力。
沟通陷入了僵局,生产无法继续,交期却很急。
小齐一时着急上火,却感觉无能为力。
这不夜里11点了,还一个人坐在车里,抑郁抑郁。
正在迷茫中的小齐,突然听到DuangDuang敲击车窗的声音,抬头一看,就发现佳妮手里拿着两瓶雪花,瞪着一双水汪汪的大眼睛,笑咪咪的说道:“兄弟,没有什么事是一瓶雪花摆不平的,我想喝酒了,来,走一个。”
小齐看到喜欢已久的女神,一时呆在车内。
佳妮说:“还愣着干嘛呀,有人能陪你喝雪花,却不一定能陪你闯天涯。而我两者都能。兄弟说说你的故事吧,看把你愁得,这可不是我心目中乐观的小齐。”
这一刻,小齐平静的心湖里开始波涛汹涌。
板内局部有3.5/3.5mi的线宽线距。
不要看线路少,BGA里面却是没有空间移不了。

客户的层叠设计和铜厚要求:

要说这个案例的原因,还要从PCB的加工流程说起。线路板的线路加工是经过图形转移和蚀刻等主要流程加工而成。
内层线路的加工流程如下:

DES为DES为显影;蚀刻;去膜工序的简称。
下图为DES的流程:

内层蚀刻原理:是在酸性条件下把不需要的铜箔去掉。外层是碱性蚀刻流程。
从上图中我们可以看出,内层线路加工是把需要的图形用干膜或湿膜保护起来,将不需要留下来的铜箔用酸性药水蚀刻掉。
蚀刻就是用化学方法按一定的深度除去不需要的金属。
蚀刻因子:
蚀刻液在蚀刻过程中,不仅向下而且对左右各方向都产生蚀刻作用,侧蚀是不可避免的。侧蚀宽度与蚀刻深度之比称之为蚀刻因子。
侧蚀不能完全杜绝,我们只能将其降到最低。
蚀刻因子是用于考量蚀刻侧蚀量的指标,因不同成品铜厚的侧蚀量会有所差别,所以蚀刻因子是与成品铜厚有关。

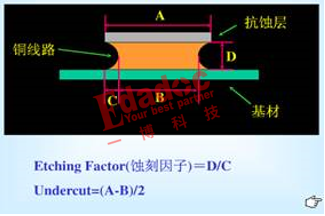
线路上的铜越厚,线路的侧蚀越严重。
发生在抗蚀层图形下面导线侧壁的蚀刻称为侧蚀,侧蚀的程度是以侧向蚀刻的宽度来表示。

我们理想中要求药水是垂直向下蚀刻的,但是现实中药水向下蚀刻的同时,也对线路的侧面有了腐蚀,通常PCB铜厚越厚,向下蚀刻的时间会越久,侧蚀量也越大。

成品后的线路由于侧蚀的影响,变成了梯形。所以在计算阻抗时,会有W1和W2的上下线宽的选项要填写。

所以为了避免蚀刻后线路变细,根据PCB成品铜厚的大小,工厂的工程制作时会依照本厂的工厂能力和蚀刻因子的大小,做一定的线路补偿,比如说我们PCB内层在1OZ铜厚时,蚀刻补偿在1mil,2OZ在2mil.如果线路在蚀刻补偿后,线路间距过小,曝光显影后,线路蚀刻时会导致线路过细或开路。
外层线路的加工过程如下:

下面为外层图形电镀和蚀刻的流程:

外层线路工序,上图中蓝色干膜保护的地方,是需要蚀刻的地方。
因为外层电镀后,铜厚增加超过了干膜厚度,在退膜工序时干膜退不掉,就形成了夹膜,本来要腐蚀掉的铜箔,因为干膜没有显影干净,部分地方就被保留下来了,比如说本来是一对差分线,中间不能有连接的,结果因为夹膜,导致铜腐蚀不完全,短路就产生了。
图形电镀后线路铜厚大于干膜厚度会造成夹膜。(一般PCB厂所用干膜厚度1.4mil),成品铜越厚,这种风险越大。
短路不良如下:

了解了上面的内外层线路的加工过程,那我们在设计时要怎么避免这种问题呢。
加大PCB线宽线距或者降低其成品铜厚。
如果考虑安规和载流的影响,无法减少成品铜厚,PCB的设计时就适当的加大线宽和线距,具体内层工艺能力如下(建议按照第一列的工艺能力设计):

外层的线宽线距如下(H表示成品铜厚):

后来经过E公司仿真部周哥多方验证,重新优化了设计,最终解决了客户的载流问题,内层铜厚按1OZ生产,满足生产加工能力,板子顺利下线。
这正是: